“If you can’t measure it, you can’t improve it.”
– Peter Drucker
The Need for Key EHS Metrics
An astounding number of companies fail to integrate consistent EHS practices into their operations. As a result, often find themselves scrambling to comply with an agency request, customer RFP or even a plaintiff’s demand. Establishing and tracking actionable metrics for EHS success is an area of challenge for many companies.
As the Peter Drucker quote highlights, knowing what is important and how to measure it, is the key to improvement. As another year ends, it brings home the need for accurately measuring their EHS programs. While that sounds easy in principle, many companies lack the program visibility to effectively leverage metrics in their daily operations. Establishing key EHS Metrics is critical to measuring and improving their program.
Managerial Alignment
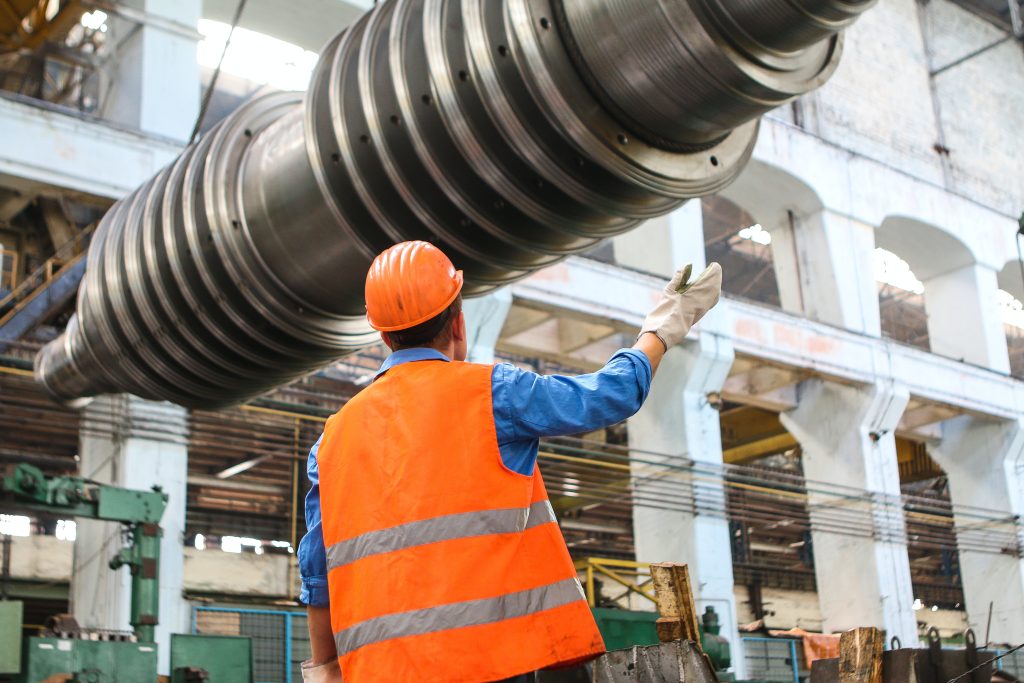
There are already so many data points that management must juggle – from sales quotas to customer service benchmarks to financial performance. Adding more metrics may seem counterproductive. The only way to truly drive improvement throughout your company culture is to ensure that management is aligned on what is important and how to measure success.
Just like any other corporate strategy, EHS excellence depends on tone at the top. If executives have actionable metrics, then companies will see a reduction in risky behaviors and an enhanced EHS focused culture.
Questions that Establish Key EHS Metrics
For EHS performance, do you know the answers to some basic questions about your company?
- What was your company’s Total Recordable Injury Rate (TRIR), number of lost workdays and number of days with employees on light duty?
- Do you know the number of site and equipment inspections done in the last 90 days?
- Do you know the most common deficiency found in these inspections?
- Do you know how many near misses were reported in the last year?
- Do you know how many injuries your company had last year by job type, and how many of those were OSHA recordable?
Preventable Re-occurrence of Incidents
There are many companies that can answer at least some of these questions and that may be fine for their business.
However, too many companies have no safety and compliance related metrics at all, while others only measure lagging indicators like injuries, penalties, and driver citations. While these are key metrics that every company should track, they only look in the “rearview mirror” and do very little to prevent reoccurrence or establish actionable improvement programs.
More sophisticated EHS programs also use leading indicators like training rates, near miss reporting, behavior observations and more to provide management with forward looking practices designed to prevent issues rather than just report them.
Data Collection and Result Distribution
Companies that have a good handle on their data, benchmarks and trends, all use some type of software system to capture the information. The key is to make data collection and result distribution easy so as not to create an administrative roadblock.
Whether you use a software tool or have manual processes, there is no doubt that in order to drive improvement and sustain long-term compliance focus, you need to establish some key EHS metrics and communicate them with your team. If you set clear targets and have your team aligned, you can consistently leverage metrics to improve your EHS culture and performance that will drive value directly to your bottom line.